
+ Grinding
+ Batch work
+ Repairs
SUBCONTRACT
PRECISION
ENGINEERING
+ CNC turning
+ Five-axis milling
+ Gear cutting
Subcontract precision CNC machining at competitive prices
As a specialist in subcontract precision CNC machining, Yorkshire-based Westin Engineering serves customers across a wide range of industries.​ Our blend of skills, experience and sophisticated machinery equips us to fulfil your requirements with the following services:
-
Manual Machining: Traditional machining methods for bespoke and precise components.
-
CNC Turning: High-precision turning for complex geometries and tight tolerances.
-
5-Axis Milling: Advanced milling techniques for intricate and multi-faceted parts.
-
Gear Cutting: Precision gear manufacturing for various industrial applications.
-
Grinding: High-accuracy grinding for superior surface finishes and dimensional accuracy.
-
Repairs: Comprehensive repair services to restore components to their original specifications.
​With a focus on quality, customer satisfaction and competitive pricing, we can produce machined parts large and small as one-offs or in batches, with a quick turnaround. In addition, we can offer in-house balancing and shot blasting services.
We also offer CAD/CAM software for offline programming allowing our experienced engineers to:
​
-
Custom Manufacture: Create parts from detailed drawings or specifications.
-
Reverse Engineering: Reconstruct parts from existing components.
-
Product Repair: Fix and restore parts to extend their service life and functionality.
Quality assurance built on more than 100 years of experience
-
The Westin name has been synonymous with industry in Huddersfield since 1921.
-
Locally and independently owned, Westin Engineering is based in a former textile mill and forms part of the Westin Engineering Group.
-
The Group includes Westin Drives​, specialists in electric motor rewinds, repairs and automation.
-
Rapid servo motor repairs are carried out by our sister company, Quality Servo Motor Repairs.

-
​We also offer industrial marine products and repairs through Westin Pumps.
-
Our ISO 9001:2015 accreditation means we put our customers first, making sure we meet their needs.
Repairing and refurbishing components from motors to pumps

A key part of our operations is the refurbishment and repair of a wide range of components. Our services include:
​
-
Remaking Motor Housings
-
Pump Head Repairs
-
Box Shaft Renewals
With a typical turnaround of one to two days, we strive to get your equipment back in service swiftly. For parts requiring manufacturing, the process may take slightly longer.
Our service extends to the repair, reconditioning and supply of: Gearboxes, geared motors, electric motors and pumps. We also specialise in rewinding electric motors of various types and sizes.
Our Huddersfield service centre has an internal lifting capacity of up to 20 tonnes, ensuring we can handle even the most substantial projects. In short, you can trust us for efficient, and expert repair and refurbishment services.
NEWS: How advanced measuring ensures quality control
Precision engineering demands exacting standards, as the smallest deviation can lead to significant consequences.
Quality control is paramount at Westin Engineering and high-quality measuring equipment plays a crucial role.
We use the latest Coordinate Measuring Machine (CMM) software which calculates the geometry of objects by sensing discrete points on the surface with a probe.
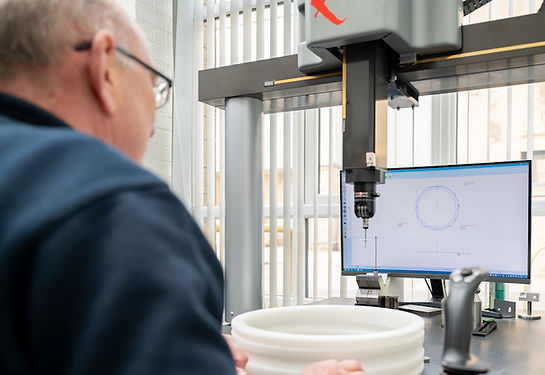
Our engineers can to measure to within five microns – five millionths of a metre – a refinement of particular value in the inspection of complex components.
What our customers say: Happy with the quality and service'
A company commissioned us to manufacture a bespoke housing and design a linking shaft to support alterations to a product line. 'We have carried out the work to fit the components and I am pleased to say we were very happy with the quality and service received, which has enabled us to complete the project.'
A customer brought a burnt-out fan motor for repair by our sister company, Westin Drives. The bearing housing end shield was cracked beyond repair.
​Since the bespoke motor couldn't be replaced off the shelf, our engineers were able to manufacture a new housing.